官网 机械加工工艺手册 第3版 第3卷 现代加工技术卷 王先逵 机械加工工艺规程设计常用金属材料及热处理技术基础知识书籍
运费: | ¥ 0.00-30.00 |
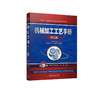
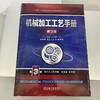
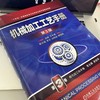
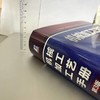
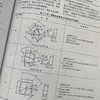
商品详情
书名:机械加工工艺手册 第3版 第3卷 现代加工技术卷
定价:399.0
ISBN:9787111719182
作者:王先逵
版次:3
内容提要:
第3版手册以机械加工工艺为主线,将数据与方法相结合,汇集了我国多年来在机械加工工艺方面的成就和经验,反映了国内外现代工艺水平及其发展方向。在保持第2版手册先进性、系统性、实用性特色的基础上,第3版手册全面、系统地介绍了机械加工工艺中的各类技术,信息量大、标准新、内容全面、数据准确、便于查阅等特点更为突出,能够满足当前机械加工工艺师的工作需要,增强我国机电产品在国际市场上的竞争力。
本版手册分4卷出版,包含加工工艺基础卷、常规加工技术卷、现代加工技术卷、工艺系统技术卷,共36章。本卷包括特种加工技术、精密加工与纳米加工技术、微细加工技术、高速切削加工技术、难加工材料加工技术、表面光整加工技术、复合加工技术、增材制造(3D打印)技术、表面工程技术、航空结构件加工工艺设计与实现。
本手册可供机械制造全行业的机械加工工艺人员使用,也可供有关专业的工程技术人员和工科院校师生参考。
作者简介:
王先逵,清华大学教授,长期从事精密和超精密加工及计算机辅助制造等先jin制造技术方面
的教学和科研工作,出版专著18部,是我国第一台数控机床(1957年)、
第一个计算机集成制造系统(1987)的主要完成人之一。
李旦,哈尔滨工业大学教授,编著出版专业教材和辅助教材7本,
主要研究方向为精密与超精密加工技术、机械加工自动化机构。
孙凤池,第一汽车集团工艺部部长、研究员,曾发表多篇论文,
擅长领域为切削加工工艺、切削刀具技术、齿轮制造工艺。
赵宏伟,吉林大学副校长、教授,2012年教育部新世纪优秀人才,
2016年获政府特殊津贴,2019年获国家杰出青年科学基金,
擅长精密仪器设计制造、仿生精密驱动、超精密加工技术及装备等领域。
张定华,西北工业大学教授,出版专(译)著5 部,发表学术论文270余篇,
其中SCI/EI 收录130 余篇,长期致力于多轴数控加工技术、航空发动机先进制造技术等方面的研究。
常治斌,湖北汽车工业学院教授,编写教材和专著4部,
主要从事机械学及汽车制造装备技术方面的教学与研究,并承担东风十堰汽车公司的项目。
目录:
目录
第3版前言
第2版前言
第1版前言
第1章特种加工技术
1.1概述3
1.1.1特种加工的定义和特点3
1.1.2特种加工的分类3
1.1.3几种常用特种加工方法性能和用途的对比4
1.2电火花穿孔、成形加工4
1.2.1电火花穿孔、成形加工的原理4
1.2.2电火花穿孔、成形加工机床5
1.我国电火花穿孔、成形加工机床的型号和标准5
2.电火花成形加工机床主要型号与技术参数5
1.2.3电火花加工用的脉冲电源5
1.基本的脉冲波形及其主回路5
2.各种派生的电火花加工用的脉冲电源5
1.2.4电火花加工的工具进给调节系统8
1.工具电极自动进给调节系统的类型8
2.自动进给调节系统的基本组成部分8
3.步进电动机自动进给调节系统9
4.直流、交流伺服电动机自动进给调节系统9
1.2.5电火花加工的工具电极和工作液系统9
1.电火花加工用工具电极材料9
2.电火花加工用工具电极的设计与制造9
3.电火花加工用的工作液系统11
1.2.6电火花加工的基本工艺规律11
1.电火花加工的工艺指标11
2.电火花加工的电规准11
3.电火花加工工艺规律及电火花加工工艺曲线图表12
1.2.7电火花加工时正确选择电规准的方法21
1.2.8电火花加工时工具电极的安装、调整和找正21
1.工具电极的安装、调整和找正的要求21
2.工具电极的安装、调整和找正的装置21
1.2.9电火花加工机床的一般故障和加工中的不正常现象23
1.液压主轴头常见的故障、原因及解决办法23
2.伺服电动机主轴头常见的故障、原因及解决办法24
3.电火花加工中的不正常现象的故障、原因及解决办法24
1.3电火花加工小孔25
1.3.1小孔的高速电火花加工25
1.3.2小深斜孔的高速电火花加工26
1.3.3异形小孔的电火花加工26
1.喷丝板异形小孔的电火花加工26
2.多个小方孔筛网的电火花加工27
1.3.4微孔电火花加工27
1.微小轴(工具电极)的制作27
2.高深径比微小孔的加工28
1.4电火花成形加工的数控技术28
1.4.1数控电火花加工机床的类型28
1.4.2电火花数控摇动加工28
1.电火花数控摇动加工的特点28
2.电火花数控摇动加工的代码和轨迹28
3.数控摇动的伺服方式29
1.5电火花加工的其他工艺形式及应用30
1.5.1电火花磨削30
1.电火花小孔磨削30
2.电火花刃磨和切割31
3.电火花对磨和跑合31
1.5.2共轭回转电火花加工及双轴回转电火花加工32
1.电火花共轭同步回转加工精密内外螺纹32
2.电火花共轭倍角同步回转加工32
3.双轴回转展成法电火花加工精密凹凸球面、平面32
1.5.3电火花表面强化及刻字34
1.电火花表面改性和强化34
2.电火花刻字35
1.5.4混粉电火花镜面加工技术35
1.混粉电火花镜面加工原理及特点36
2.混粉电火花镜面加工工艺要点36
3.混粉电火花加工装置及设备36
4.混粉电火花镜面加工应用实例36
1.5.5半导体和非导体电火花加工技术36
1.半导体和高阻抗材料的电火花加工36
2.非导体的电火花加工37
1.5.6气体介质中电火花加工37
1.气体介质中电火花加工原理37
2.气体介质中电火花加工要点37
3.气体介质中电火花三维形状加工37
1.5.7电火花铣削加工技术37
1.电火花铣削加工技术的产生及特点37
2.电火花铣削加工中的主要关键技术38
1.5.8微细电火花加工技术38
1.微细电火花加工的关键技术38
2.微细电火花加工的应用举例39
1.5.9短电弧加工39
1.短电弧加工的主要特点39
2.短电弧加工的主要适用范围40
3.短电弧加工应用实例40
1.6电火花线切割加工40
1.6.1电火花线切割加工原理和特点40
1.6.2双向高速、单向低速走丝电火花线切割加工比较40
1.6.3电火花线切割机床42
1. 电火花线切割机床的分类及型号42
2. 电火花线切割机床标准42
3. 我国生产的主要电火花线切割机床42
4. 国内外生产的主要电火花线切割机床42
1.6.4导轮部件及电极丝保持器42
1.导轮部件42
2.电极丝保持器46
1.6.5电火花线切割机床夹具和加工工件装夹方法46
1.电火花线切割机床夹具46
2. 电火花线切割加工工件的装夹方法46
1.6.6常用电火花线切割电源49
1. 常用电火花线切割电源的波形、电参数及性能49
2. 电火花线切割电源波形和电参数对工艺指标的影响49
1.6.7电火花线切割工艺效果分析50
1.高速走丝速度vs对切割速度vwi的影响50
2.电极丝材料及直径对线切割工艺效果的影响50
3.工件厚度h对切割速度vwi的影响51
4.电极丝往复运动引起的黑白条纹和斜度52
5.不同工作液对工艺参数的影响52
6.不同电参数对线切割表面熔化层的影响52
7.单向低速走丝电火花线切割工艺效果52
1.6.8线切割引起断丝的原因54
1.6.9线切割加工中工件产生的变形和裂纹55
1.产生变形和裂纹的规律55
2.减小变形和裂纹的措施55
1.6.10线切割机床的扩展运用56
1.用普通线切割机床加工带斜度凹模的简易方法56
2.用两轴控制加工三维曲面56
1.6.11编制简单零件线切割加工程序的方法58
1.程序格式58
2.零件编程实例62
3.有公差编程尺寸的计算法62
4.间隙补偿值f63
1.6.12线切割自动编程65
1.人机对话式自动编程65
2.语言式自动编程65
3.图形交互式自动编程66
1.7电化学加工67
1.7.1电化学加工原理及设备组成67
1.电化学加工原理67
2.电化学加工用电源69
3.电化学加工的分类70
1.7.2电解加工71
1.电解加工的特点及其应用71
2.电解加工的设备72
3.电解加工的基本规律74
4.电解加工的阴极设计77
5.电解加工的电解液80
6.混气电解加工83
7.脉冲电解加工84
8.小孔束流电解加工84
9.数控展成电解加工 84
10.旋印电解加工85
11.电解线切割加工86
12. 电解加工的应用86
13.电解加工常见疵病、产生原因及消除方法86
1.7.3电化学抛光86
1.影响电化学抛光的主要因素86
2.金属的电化学抛光工艺及应用91
1.7.4电解磨削93
1.电解磨削的加工原理93
2.电解磨削用的电解液94
3.电解磨床及改装95
4.电解磨削的工艺参数95
5.电解研磨95
1.7.5在线电解修锐镜面磨削(ELID)96
1. ELID磨削技术的优点96
2. ELID磨削装置96
1.8超声加工97
1.8.1超声加工的原理及特点97
1.8.2超声加工的设备组成97
1. 超声加工设备的规格与技术性能98
2.振幅变幅杆(扩大棒)的设计、计算和工具长度的确定98
1.8.3超声加工的基本工艺规律101
1.超声加工的加工速度101
2.超声加工的加工精度101
3.超声加工的表面粗糙度102
1.8.4超声加工的应用103
1.打孔、套料与切断103
2.旋转超声加工103
3.超声清洗加工104
4.超声焊接105
5.超声辅助加工105
6.难加工材料、复合材料的超声加工106
1.9高能束加工106
1.9.1激光加工106
1.激光加工的原理及特点106
2.激光加工的设备组成106
3.激光切割的工艺参数109
1.9.2电子束加工110
1.电子束加工的原理及特点110
2.电子束加工的工艺规律111
3.电子束加工的应用111
1.9.3离子束加工111
1.离子束加工原理及其特点111
2.离子束加工的应用113
1.10化学加工114
1.10.1化学铣切加工114
1.化学铣切的特点114
2.化学铣切的缺点114
3.化学铣切的应用范围114
4.化学铣切的主要过程114
1.10.2光化学腐蚀加工115
1.10.3化学抛光115
1.11水喷射切割116
1.11.1水喷射切割加工的基本原理及特点116
1.11.2水喷射切割加工的基本工艺规律116
1.11.3水喷射切割加工的应用117
1.12磨料喷射加工117
1.12.1磨料喷射加工的基本原理117
1.12.2磨料喷射加工的基本工艺规律117
1.12.3磨料喷射加工的应用119
1.13复合加工119
1.13.1关于复合加工的一般概念119
1.13.2超声-电火花复合加工119
1.超声-电火花复合加工的原理119
2.超声-电火花复合加工的影响因素119
3.超声-电火花复合加工的应用举例120
1.13.3电解-电火花复合加工120
1.13.4超声-电解复合加工120
参考文献121
第2章精密加工与纳米加工技术
2.1概述125
2.1.1精密加工与超精密加工的概念、范畴、特点和分类125
1.精密加工与超精密加工的概念125
2.精密加工和超精密加工的特点125
3.精密加工和超精密加工方法及其分类126
2.1.2精密加工和超精密加工原理128
1.进化加工原理128
2.微量加工原理128
2.1.3精密加工和超精密加工的工艺系统129
1.影响精密加工和超精密加工的工艺因素129
2.精密加工和超精密加工的工艺系统结构129
2.1.4精密加工和超精密加工技术的地位、作用和发展129
1.精密加工和超精密加工技术的地位和作用130
2.精密加工和超精密加工技术的发展130
2.2金刚石刀具超精密切削加工130
2.2.1金刚石刀具超精密切削机理130
1.金刚石刀具超精密切削的切屑形成130
2.加工表面的形成及其加工质量130
3.表面破坏层及应力状态131
2.2.2金刚石刀具的设计和刃磨131
1.金刚石的性能和结构131
2.金刚石刀具的设计133
2.2.3金刚石刀具超精密切削的工艺规律138
1.影响金刚石刀具超精密切削的因素138
2.金刚石刀具超精密切削工艺138
2.2.4金刚石刀具超精密切削的应用和发展140
2.3精密和超精密磨削加工141
2.3.1精密磨削加工141
1.普通砂轮精密磨削机理141
2.普通砂轮精密磨削砂轮选择142
3.精密磨床的选择142
4.普通砂轮精密磨削时的砂轮修整142
5.普通砂轮精密磨削时的磨削用量143
2.3.2超硬磨料砂轮精密磨削143
1.超硬磨料砂轮精密磨削特点及应用143
2.超硬磨料砂轮精密磨削机理144
3.超硬磨料砂轮精密磨削用量选择144
4.超硬磨料砂轮磨削时的磨削液选择144
5.超硬磨料砂轮修整144
2.3.3超精密磨削加工146
1.超精密磨削的概念、机理、特点及其应用146
2.超硬磨料微粉砂轮146
3.超精密磨床146
4.超精密磨削工艺147
2.3.4精密砂带磨削148
1.精密砂带磨削方式、特点和应用范围148
2.精密砂带磨削机理148
3.精密砂带磨床和砂带磨削头架(装置)148
4.精密砂带磨削工艺148
2.4精密光整加工149
2.4.1研磨加工149
1.传统研磨加工的概念、分类、特点及应用范围149
2.研磨机理和加工要素150
3.精密和超精密研磨方法151
2.4.2抛光加工151
1.抛光加工机理和加工要素151
2.抛光和研磨复合加工 152
3.精密和超精密抛光方法152
2.4.3珩磨156
1.珩磨加工原理、特点和应用范围156
2.珩磨头156
3.珩磨工艺要素选择157
4.新型珩磨加工方法157
2.4.4超精加工158
1.超精加工的原理、特点及其应用范围158
2.超精加工头158
3.超精加工工艺要素选择158
4.超精研抛159
2.4.5挤压研抛159
1.挤压研抛原理及应用159
2.挤压研抛的工作要素160
2.4.6砂带振动研抛160
1.砂带振动研抛原理160
2.砂带振动研抛运动轨迹160
2.4.7喷射加工161
1.喷射加工的原理和类型161
2.喷射加工的工艺因素161
3.喷射加工的应用161
2.4.8滚磨加工161
1.涡流式滚磨加工161
2.振动式滚磨加工161
3.离心式滚磨加工162
4.主轴式滚磨加工162
2.5微细加工162
2.5.1微细加工的概念和特点162
1.微细加工的概念162
2.微细加工的特点162
2.5.2微细加工机理162
1.微细加工的精度表示方法162
2.微细加工机理162
2.5.3微细加工方法163
1.微细加工方法的分类163
2.高能束加工方法164
3.光刻加工技术167
4.光刻-电铸-模铸复合成形技术(LIGA)168
5.大规模集成电路的制作技术169
2.6精密机床和超精密机床170
2.6.1超精密机床的精度指标和类型170
1.超精密机床的精度指标170
2.超精密机床的类型170
3.超精密机床的结构特点170
2.6.2超精密机床的设计171
1.精密主轴部件171
2.导轨174
3.进给驱动装置177
2.6.3超精密加工机床的状况180
1.国内外超精密机床的状况180
2.典型超精密加工机床180
2.7精密测量与误差补偿183
2.7.1概述183
1.测量技术发展与加工精度的关系183
2.检测方式183
3.测量仪器与测量环境183
2.7.2精密检测方法184
1.圆度和回转精度测量184
2.直线度和平面度的检测186
3.定位精度检测187
4.表面粗糙度的测量189
2.7.3微尺寸测量技术189
1.微细图形尺寸的测量192
2.电子显微镜测量193
2.7.4误差补偿技术193
1.概述193
2.误差补偿的类型194
3.误差补偿过程及其系统194
4.典型误差补偿系统194
2.8精密定位、对准和微位移技术196
2.8.1精密定位196
1.定位的概念196
2.精密定位的方式196
2.8.2对准196
1.对准的概念196
2.对准的方法196
2.8.3微位移技术196
1.微位移系统196
2.微位移装置的类型197
3.典型微位移工作台198
2.9纳米加工技术200
2.9.1概述200
1.纳米加工的方式200
2.纳米加工方法200
3.纳米加工技术与纳米技术的关系201
4.纳米材料的性能201
2.9.2扫描探针显微加工技术201
1.扫描探针显微加工原理201
2.扫描探针显微加工方法202
2.9.3纳米级测量技术202
- 机械工业出版社旗舰店 (微信公众号认证)
- 扫描二维码,访问我们的微信店铺
- 随时随地的购物、客服咨询、查询订单和物流...